The controller is the brain of an irrigation system. It automates the irrigation of a field crop, greenhouse, fruit or vegetable, green house, urban trees, park and garden, etc...
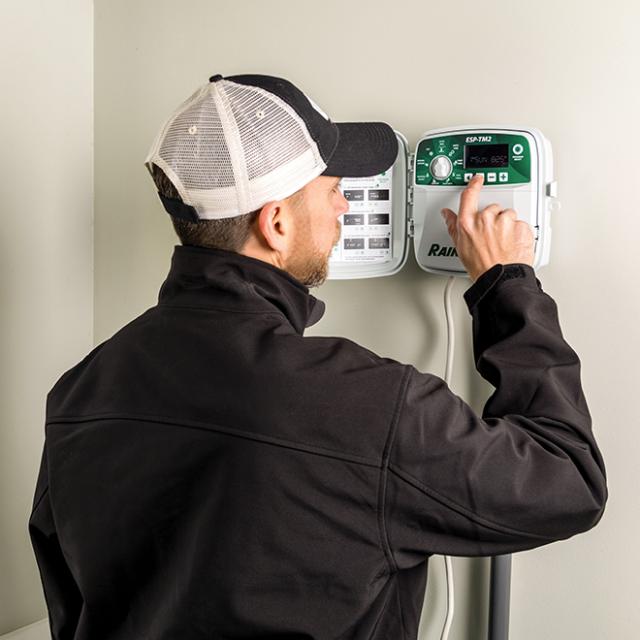
Definition:
The controller is the brain of an irrigation system. It automates the irrigation of a field crop, greenhouse, fruit or vegetable, green house, urban trees, park and garden, etc...
The first layer or basic function performs output tasks. A unique task, like one-way of a pivot on a button clic, until a "defect" occurs, like a stop. Up to thousands of tasks on a horticultural computer. The input layer also collects machine data : voltage, pressure, position, alert ..
On an orchard controller, the sequence is cyclical: the tasks are repeated, defining the days "on" over the week for example, the start times and irrigation durations, for different sectors. It replaces manual action to open and close valves. This loop can take place over the entire season, if no interruption or modification occurs. In sequential programming, the system connects, at agreed time, the first solenoid valve, then closes it the end of the programmed time. Then moves to the second sector for the same or different duration, and so on.
Unless an external event interrupts or modifies the process, according to 2 concepts, transposable to our irrigation world :
- in a closed loop, information from the external environment can regulate, modify, reprogram. A logical or software input, through sensors that provide real-time environmental data : soil moisture, rain, meteorological parameters, allowing to adjust dynamically or manually the current program.
- in an open loop, the machine would perform tasks without taking into account external variations.
The second layer of the controller is the human-machine interface (HMI).
On the user side, depending on models, means enter time slots in orchard program as described above, or simply press a button on an electromechanical system, up to enter necessary data for a sophisticated program.
On manufacturer's side, the PLC of a lateral for example, can require programming of 32 digital inputs and 4 analog inputs, to allow control 16 digital outputs (0/1) and 4 analog outputs (4-20 mA). As well as installing the corresponding sensors on the machine, ensuring the long-lasting smooth operation of the whole. For a manufacturer of electro-mechanical pivot cabinet, the wiring of about ten logical ports is necessary. For most of the current models on the market, the manufacturer’s design office has mastered its electronic board and programming. For the most sophisticated computer systems, the manufacturer compiles a complete computer code that can include tens of thousands of lines. The HMI of most models provides a manual replacement function, allowing to start or stop manually, apart from programming logic.
HMI will be deeply influenced by the third layer.
The third layer is communication or connectivity, when the programmer becomes a connected object. The manufacturer then uses radio frequency ranges, for example in Europe: 433 MHz, 868 MHz (dedicated system, LoRa, Sigfox), GSM 2G in 900 Mhz, 3G in 900, 1900 and 2100 MHz, 4G in 800 and 1800 MHz, 5G in 700, 3500 MHz and 26 GHz. With different communication protocols (MQTT, HTTP, CoAP, AMQP, Bluetooth, etc.) as well as different protocols: Modbus, MQTT, LoRaWan, Zigbee, WI-FI, LTE-M, NB-IOT. At the other end, the user gets telemetry (measurements) remote management (decisions) remote control (actuate) via internet/ app or platform. Using smartphone, tablet or computer, with internet browser. Either indoors on the office or home box, or outdoors via 4G, 5G often available. This third layer of communication allows to remotely handle the second layer (machine interface) in order to interact with the first layer (functions). Start, slow down, stop a machine remotely, follow data from the machine : electrical, hydraulic, mechanical (voltage, pressure, position, etc.) This, in a more or less sophisticated environment, which is the fourth layer.
The fourth layer is the WEB platform, which presents the information. If we take the example of the Comsag solution in orchards, the platform proposes a synoptic of the irrigation network, and a choice beetween pre-established irrigation programs. Upstream data are machine parameters, reporting actual events, as well as sensor measurements, used by decision tools. Downstream data allow the storage, execution and replacement of the valve opening-closing program.
If we take the example of Fieldnet by Lindsay, the platform geolocates the pivots of a farm, displays them as active icons for remote management. Means by clicking on the icon, one obtains the information from machine and remotely actuates it.
Selection criterion for a controller ?
The first criterion is the optimization of the final cost of the entire installation, where the controller is a key, a master piece.
The controller market is mature, the cost/ profit ratio is efficient. An offer of a few hundred euros in arboriculture and horticulture, a few thousands on larger facilities.
The final cost of the installation, allowed by a controller will guide the designer’s offer or the choice of the irrigator.
The second important criterion is a feeling of mastering programming. For the installer, a reliable model that he masters, that he is able to explain, to troubleshoot.
For the irrigator : understanding, reprogramming easily, without discomfort in high season.
Depending on the model: in-person or via a smartphone, an application, internet.
The agronomic specifications, that is to say the response to the needs of adaptation to the field, unfortunately intervene in a rather succinct way in the initial investment choices.
In general, the water balance or current practice is at the origin of the overall hydraulic plan (sizing, diameters, flows, etc.). It is often a question of automating known tasks, known practices, without significant evolution at this stage, often using inches as a unit of measurement, which leads to volume in an operational way. The possibilities of the equipment and its good use will then make the difference.
AC/DC: the power supply is a determining criterion in the choice of model.
The power grid can be available at the pumping station or around the farm in horticulture, market gardening, greenhouse or shelter.
An AC controller (on mains, 380, 220 V AC) can be a cabinet, a PLC, a greenhouse computer, a 24VAC orchard programmer, with wired solenoid valves, if the cable is cheaper than wireless.
In green space and golf, one can connect many valves on 2 wires only, thanks to decoders.
When the power grid is not accessible, the lowest cost may lean towards DC controllers, such as battery-operated standalone valves.
Same case when water is available under pressure on a collective network or a private network maintained under pressure thanks to a balloon, a presostat and a pump with electronic variation.
Centralization of programming, made possible by communication.
By definition, information is centralized in a single point in a cabinet, multi-way AC programmer, computer.
By definition, the information is dispersed in the case of a network of battery controllers (DC), wireless solenoid valve network, and must be re-centralized on an application, via a up and down communication. For example, Solem splits the intelligence between the valve module and the platform. The module runs its embedded program, editable from the platform. The sensors are processed at the module level in order to send alerts to the platform, which processes them and drops an on/ off instruction back to the module for its current program.
Acknowledgements to Fanny Abrahamse (director & electrotechnician Eaux Vives) Michel Contardo (director TCSD) Laurent Denieulle (Debernard Irrigation) Michaël Fayaud (director Urbasense) Stephan Tuffery (Solem)